A solid understanding of PCB materials and their applications is crucial for anyone in the design and manufacturing of printed circuit boards. These materials, each with unique properties, advantages, and limitations, play a significant role in the performance, reliability, and cost-effectiveness of the final product. This guide provides an overview of the most common materials used in PCB construction and their respective applications, alongside insights into the importance of surface finishes and coatings.
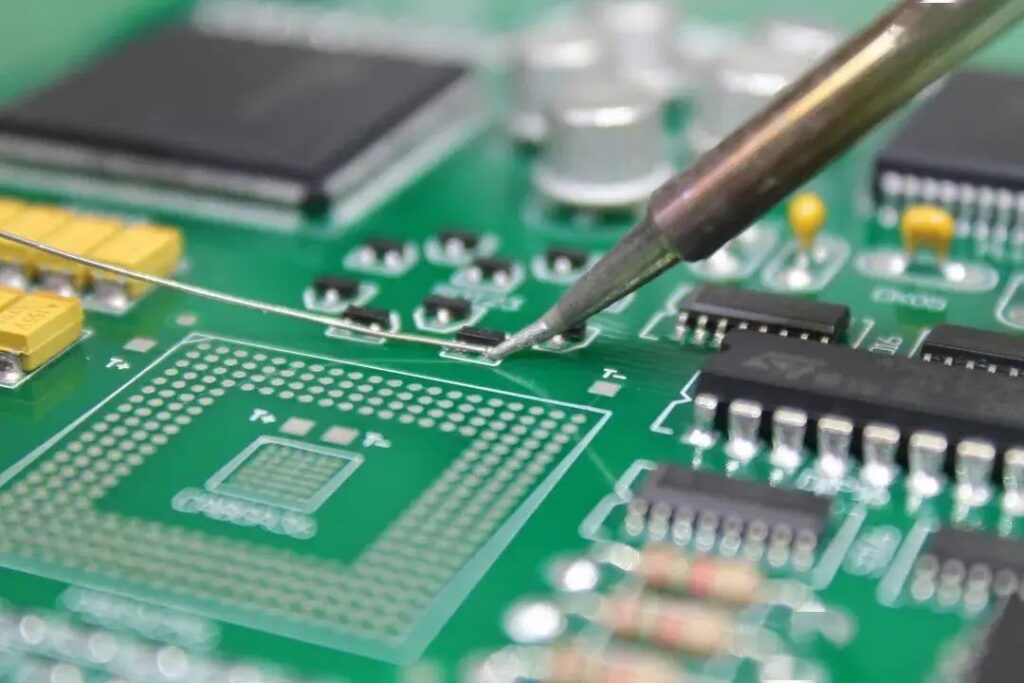
Common PCB Materials
FR4 – A Popular Choice
The most prevalent material used in PCB construction is FR4, a fiberglass-reinforced epoxy laminate. Renowned for its high thermal stability, mechanical strength, and resistance to moisture and chemicals, FR4 is widely utilized in consumer electronics, automotive, and industrial control systems. Despite its popularity, FR4 presents limitations like relatively high cost and limited flexibility.
FR5 – Enhanced Strength and Temperature Resistance
FR5, a fiberglass-reinforced polyimide laminate, shares similarities with FR4 but offers a higher temperature rating and improved mechanical strength. It is commonly employed in high-reliability applications, such as aerospace and defense, where the PCB must endure extreme temperatures and mechanical stress.
Specialty PCB Materials
Ceramic PCBs for High-Frequency Applications
Ceramic PCBs, or ceramic substrates, combine ceramic and metal materials. These PCBs are frequently used in high-frequency applications, including microwave and radio frequency (RF) devices. Their high dielectric constant and low loss tangent make them ideal for these specialized uses.
Silicon PCBs for High-Power Applications
Silicon PCBs, or silicon substrates, are constructed from silicon and metal materials. They are well-suited for high-power applications like power supplies and motor control systems, thanks to their high thermal conductivity and mechanical strength.
Metal PCBs for High-Reliability Applications
Metal PCBs, also known as metal-backed PCBs, consist of metal and other materials. These PCBs are preferred in high-reliability applications, such as aerospace and defense, due to their superior thermal conductivity and mechanical strength.
Surface Finishes and Coatings
Understanding surface finishes and coatings is critical in PCB design, as they can influence electrical performance, thermal conductivity, and mechanical strength. Common surface finishes and coatings include tin, lead, and gold, alongside various solder mask types and silkscreen options.
Conclusion
A thorough grasp of PCB materials and their applications is essential for designers and manufacturers in the PCB industry. By selecting the appropriate material and surface finish for the specific application, professionals can ensure that their PCBs meet the necessary performance, reliability, and cost criteria.
FAQs
Q: What is FR4, and why is it commonly used in PCB design?
A: FR4 is a fiberglass-reinforced epoxy laminate known for its high thermal stability, mechanical strength, and resistance to moisture and chemicals, making it a popular choice in various applications.
Q: How does FR5 differ from FR4?
A: FR5 is similar to FR4 but offers a higher temperature rating and improved mechanical strength, making it suitable for high-reliability applications like aerospace and defense.
Q: What are the benefits of using ceramic PCBs?
A: Ceramic PCBs have a high dielectric constant and low loss tangent, making them ideal for high-frequency applications such as microwave and RF devices.
Q: When should silicon PCBs be used?
A: Silicon PCBs are best suited for high-power applications, such as power supplies and motor control systems, due to their high thermal conductivity and mechanical strength.
Q: Why are surface finishes and coatings important in PCB design?
A: Surface finishes and coatings affect the PCB’s electrical performance, thermal conductivity, and mechanical strength, influencing the overall reliability and efficiency of the board.