The Main Difference between PCB and PCBA Board
We provide PCBA board services, you need to first understand what is PCB and what is PCBA.
PCB (Printed Circuit Board): This is the blank board. It’s essentially a thin laminate sheet made of insulating material (often fiberglass) with copper tracks etched onto its surface. These tracks form the electrical pathways that connect electronic components. A PCB is like a bare skeleton waiting to be brought to life.
PCBA (Printed Circuit Board Assembly): This is the completed board. It’s the PCB with all the electronic components soldered onto it, such as resistors, capacitors, integrated circuits (ICs), connectors, etc. The PCBA board is the final product that can be used in electronic devices. You can think of it as the skeleton with all the muscles, organs, and nervous system attached, ready to function.
Here’s a table summarizing the key differences:
Feature | PCB | PCBA |
---|---|---|
Components | No electronic components | Contains electronic components soldered onto the board |
Function | Provides electrical pathways | Functional electronic circuit |
Stage | Unfinished product | Finished product |
Analogy | Bare skeleton | Complete body with organs |
Here are some additional points to consider:
- Manufacturing Process: PCBs are manufactured through a subtractive process where unwanted copper is etched away from the laminate sheet. PCBA boards involve additional steps like component placement, soldering, and quality control.
- Functionality: A PCB by itself cannot perform any electrical functions. It needs the electronic components of a PCBA board to become operational.
- Applications: PCBs are used in various stages of electronics development, from prototyping to pre-populated boards for assembly. PCBA boards are the final product used in all electronic devices, from smartphones to televisions.
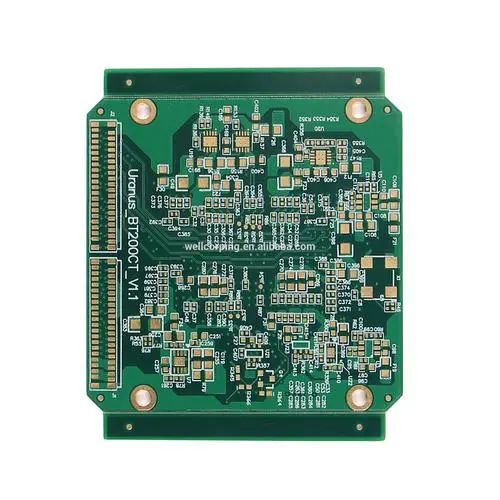
PCB
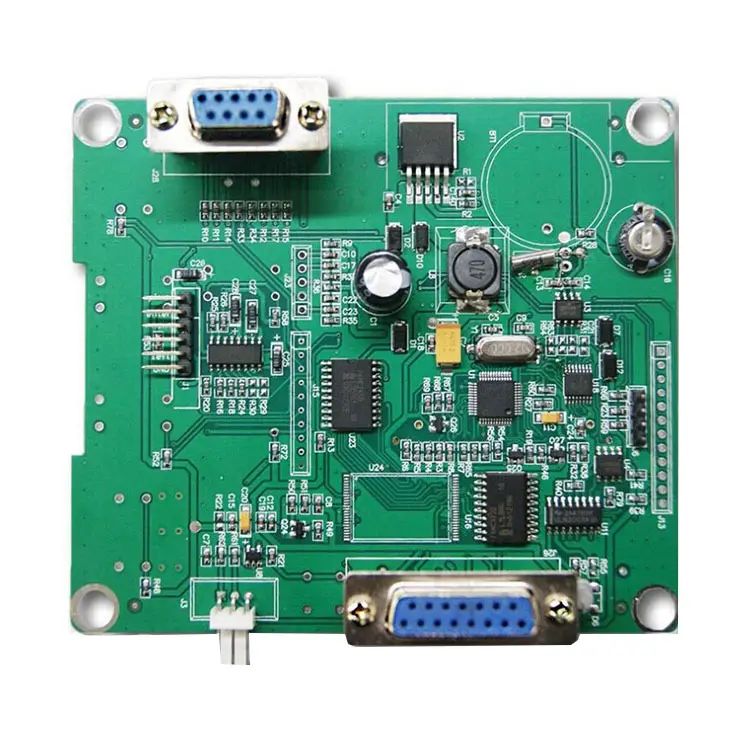
PCBA Board
High temperature ceramic PCB
Today, with the rapid development of electronic technology, ceramic PCB (ceramic printed circuit board), as a high-performance electronic component, is showing its unique charm and broad application prospects. Ceramic PCBs have excellent thermal conductivity, excellent electrical properties, excellent mechanical strength and chemical resistance, and play a vital role in high-end fields such as aerospace, military, automotive electronics and telecommunications. With the continuous advancement of technology and the increase in market demand, ceramic PCB is entering a golden age of development.
Advantages and Disadvantages of Ceramic PCBs
Advantages:
- High resistance: Reduces current loss and heat generation.
- Excellent high-frequency performance: Suitable for high-frequency communication and signal processing applications.
- High thermal conductivity: Effective heat dissipation prevents overheating.
- Excellent chemical stability: Resistant to chemical corrosion, ensuring long-term stability.
- Mechanical strength: Resistant to vibration, high temperature and high pressure.
- Precision of internal circuits: Maintains high precision and stability during manufacturing.
- High current carrying capacity: Handles larger currents with minimal temperature rise.
- Excellent heat dissipation: Low thermal expansion coefficient and shape stability enhance heat dissipation.
- Excellent insulation properties: Provides high-voltage resistance and ensures safety.
- Strong bonding: Strong bonding between copper foil and ceramic substrate prevents delamination.
Disadvantages:
Brittleness: More likely to break when subjected to shock or vibration, only suitable for small area boards.
High cost: The cost of manufacturing ceramic materials is high, making ceramic PCBs more expensive and mainly used in high-end products.
Future Development Trends of Ceramic PCBs
1. Performance Enhancement:
Higher performance: Improve thermal conductivity, insulation and mechanical strength through advanced ceramic materials such as silicon nitride (Si3N4).
Multifunctional integration: Combine traditional circuit functions with sensing, heat dissipation, energy storage and other functions.
2. Miniaturization and Integration:
Reduce size: Adapt to the trend of smaller and more integrated electronic devices.
Improve integration: Higher density interconnect (HDI) can integrate more components.
3. Green and Sustainable Development:
Environmentally friendly materials: Emphasize environmental sustainability through clean production processes.
Green manufacturing: Focus on energy conservation and emission reduction, and resource recycling.
4. Intelligent Manufacturing and Customization:
Intelligent Manufacturing: Realize highly automated and intelligent production, improve efficiency and quality.
Personalized customization: Meet diverse market needs through customized production.
5. Technological Innovation:
New Material Development: Develop advanced materials with higher thermal conductivity, lower dielectric constant and lower loss tangent.
Artificial Intelligence Integration: Use artificial intelligence to achieve intelligent and efficient manufacturing processes.
Conclusion
The future development direction of ceramic PCBs will focus on performance improvement, miniaturization and integration, green and sustainable development, intelligent manufacturing and personalized customization, technological innovation, etc., to promote ceramic PCBs to play a more important role in the electronics industry and inject new vitality into the development of the electronics industry.
One-stop PCBA Board Service
PCB Board Design Services
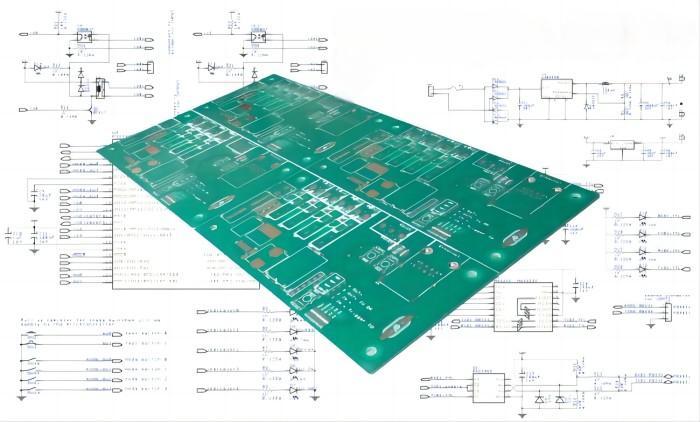
Our team of seasoned PCB design professionals possesses the know-how to navigate the complexities of PCB layout, ensuring optimal performance, manufacturability, and adherence to industry standards. We employ cutting-edge design tools and meticulous attention to detail to craft PCBs that meet your exacting requirements.
Partner with us and experience:
- Streamlined Design Process: Seamlessly transform your circuit schematics into a fully functional PCB layout.
- Unmatched Expertise: Leverage our extensive knowledge to optimize your PCB for performance and manufacturability.
- Rigorous Quality Control: Eliminate design flaws and ensure the highest quality standards through comprehensive checks.
- Accelerated Time to Market: Bring your products to market faster with efficient design and production processes.
Our comprehensive PCB fabrication and services provide a seamless solution, from concept to creation. Our team of seasoned professionals utilizes cutting-edge technology and adheres to stringent quality control standards to deliver PCBs that exceed your expectations.
Partner with us and experience:
- Expert PCB Design and Fabrication: Leverage our expertise to transform your circuit ideas into high-performance PCBs.
- Unmatched Quality Control: Implement rigorous quality checks throughout the process to ensure PCBs meet your exacting standards.
- Scalable Solutions: Cater to your production needs, from small-volume prototypes to high-volume manufacturing runs.
- Global Reach: Deliver PCBs seamlessly to your doorstep, wherever your business operates.
PCB Fabrication and Services
Electronic Components Purchasing
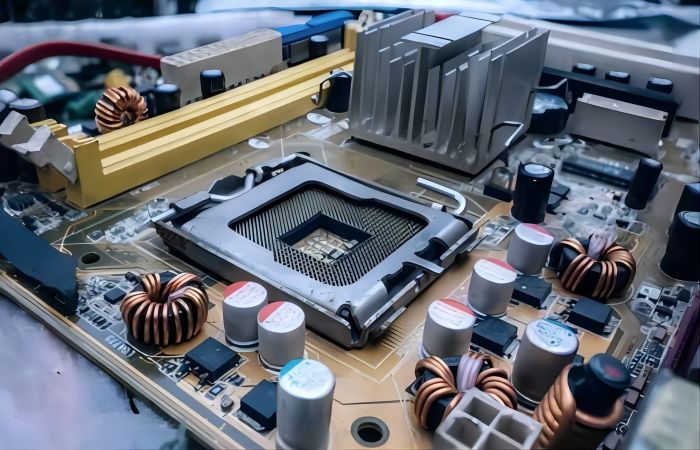
With the professional procurement team and the supply chain advantages of the Guangdong-Hong Kong-Macao Greater Bay Area, we provide BOM cost optimization, risk control, alternative material suggestions, complete BOM procurement and other services to hundreds of customers every year. Professional BOM engineers, procurement engineers and IQC incoming material quality inspection control material quality from the source, eliminating the quality risk of self-purchased materials for customers, reducing procurement costs, shortening procurement cycles, and providing strong support for customers’ R&D proofing and small and medium-sized batch production. We have established long-term cooperative relationships with many domestic and foreign electronic component manufacturers and brand authorized agents to solve customers’ procurement needs for scarce materials and multiple batches of various types of materials.
Equipped with a variety of electronic component testing equipment, we strictly test in accordance with relevant technical document standards and internal material inspection instructions to ensure that all materials entering the production line meet quality standards. The electronic component warehouse is kept at a constant temperature and humidity, anti-static control, clean, ventilated, and free of corrosive gases, to ensure material safety in all aspects. The ERP material management system is traceable in quality, and the “first in, first out” principle of materials is used to prevent dead and expired materials. We always have mainstream brand resistors, capacitors, inductors, magnetic beads, connectors, crystal oscillators, diodes and triodes and other electronic components in stock, with fast quotes and more stable prices, which greatly reduces production waiting time and helps customers build a complete electronic manufacturing ecosystem. At Gaotuo, customers can easily control the complex supply chain, convenient supply chain management services and highly competitive one-stop electronic manufacturing services, allowing customers to quickly go from solutions to final products and shorten time to market.
Our comprehensive PCBA Board assembly services provide a seamless solution, from component procurement to final testing. Our team of experienced professionals utilizes cutting-edge technology and adheres to stringent quality control standards to deliver PCBs that meet your exacting requirements.
Partner with us and experience:
- Expert PCB Assembly: Leverage our expertise to assemble PCBs with precision, accuracy, and efficiency.
- Unparalleled Quality Control: Implement rigorous quality checks throughout the assembly process to ensure PCBs meet your exacting standards.
- Scalable Solutions: Cater to your production needs, from small-volume prototypes to high-volume manufacturing runs.
- Global Reach: Deliver PCBs seamlessly to your doorstep, wherever your business operates.
PCBA Board Assembly
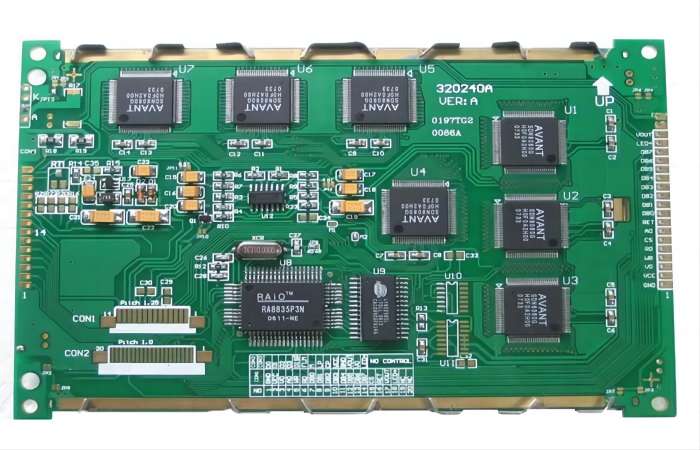
PCBA Board Application Areas
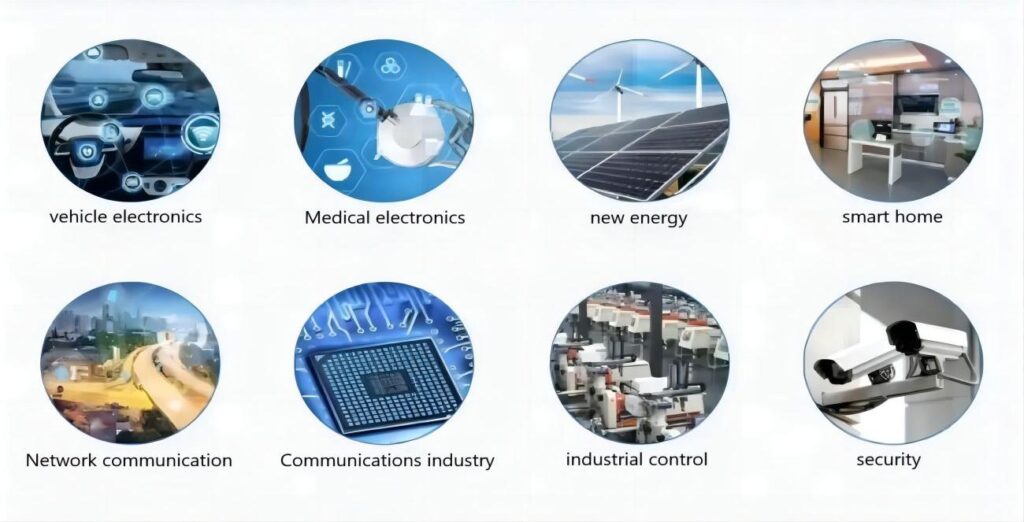
FAQs About PCBA Board (Printed Circuit Board Assembly)
PCBA stands for Printed Circuit Board Assembly. It refers to the process of assembling electronic components onto a printed circuit board (PCB) to create a functional electronic device. The PCBA process typically involves several steps, including:
- Solder paste application: Solder paste is applied to the PCB pads where components will be mounted.
- Component placement: Electronic components are placed onto the PCB according to a predetermined design.
- Soldering: The PCB is heated to melt the solder paste, forming electrical connections between the components and the PCB pads.
- Inspection and testing: The assembled PCB is inspected for defects and tested to ensure it is functioning correctly.
PCBA offers several benefits over other methods of electronic assembly, including:
- Increased efficiency and productivity: PCBA processes can be automated, leading to faster and more consistent assembly times.
- Improved quality and reliability: Automated PCBA processes help to reduce human error and ensure that components are soldered correctly.
- Reduced costs: PCBA can be more cost-effective than manual assembly, especially for high-volume production runs.
- Miniaturization: PCBA processes allow for the assembly of smaller and more complex electronic devices.
There are two main types of PCBA:
- Through-hole technology (THT) PCBA: In THT PCBA, the leads of electronic components are inserted into holes in the PCB and then soldered to the pads on the other side of the board.
- Surface-mount technology (SMT) PCBA: In SMT PCBA, electronic components are soldered directly to the surface of the PCB
When choosing a PCBA manufacturer, it is important to consider the following factors:
- Experience and expertise: The manufacturer should have experience in assembling the types of PCBs you require.
- Quality control: The manufacturer should have a robust quality control system to ensure that your PCBs are assembled to your specifications.
- Turnaround time: The manufacturer should be able to meet your production deadlines.
- Cost: The manufacturer should be able to offer competitive pricing.
- Customer service: The manufacturer should provide good customer service and be able to answer your questions and concerns promptly.
The future of PCBA is likely to see continued advancements in automation, miniaturization, and the use of new materials and technologies. Some of the key trends include:
- The use of more advanced soldering techniques, such as selective soldering and laser soldering.
- The increased use of miniaturized components, such as microchips and passives.
- The development of new materials, such as flexible PCBs and conductive inks.
- The use of additive manufacturing techniques to create PCBs.
A PCBA board is a printed circuit board (PCB) that has been assembled with electronic components such as resistors, capacitors, and integrated circuits. The board is ready for installation in electronic devices.
Important factors of designing a PCBA board include component selection, board layout, signal integrity, thermal management, power distribution, and compliance with industry standards like IPC, to ensure the board performs reliably and efficiently in its intended application.
Common quality control methods for PCBA boards include visual inspection, automated optical inspection (AOI), X-ray inspection, in-circuit testing (ICT), and functional testing to ensure the assembly meets design specifications and is free of defects.