Introduction
PCB assembly and soldering techniques are essential components of the printed circuit board (PCB) manufacturing process. Serving as the foundation for countless electronic devices, from simple calculators to complex computers, PCBs require meticulous assembly and soldering to ensure high-quality boards that meet strict specifications. This guide explores the various techniques and materials involved in PCB assembly and soldering, highlighting their roles in producing reliable and efficient electronic components.
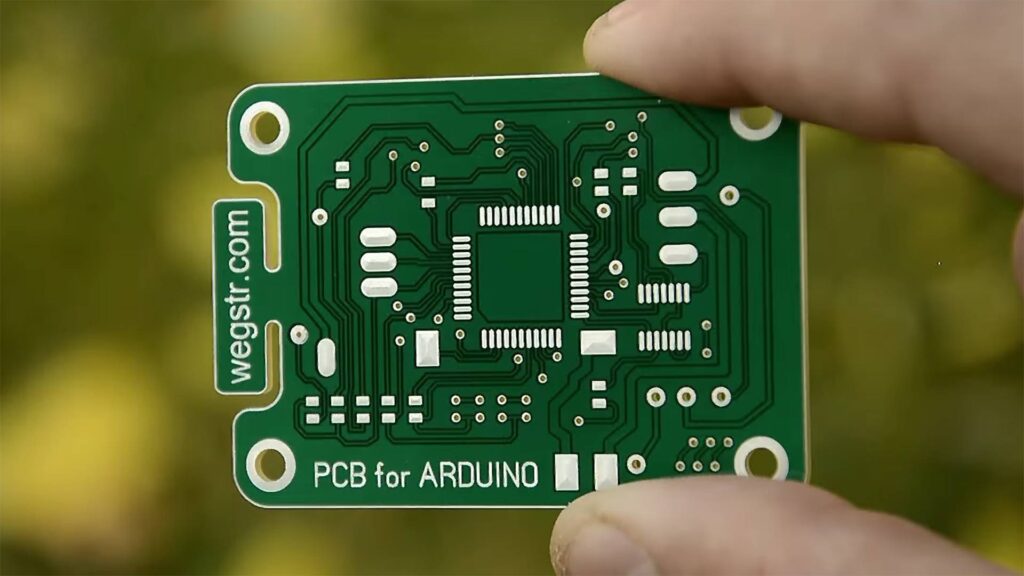
Component Placement
Precision in Positioning
The first step in PCB assembly is the placement of components onto the board. This process involves accurately positioning each component, such as resistors, capacitors, and integrated circuits, on the board’s surface. Both manual and automated techniques are employed, with automated placement machines becoming increasingly prevalent in modern manufacturing. These machines significantly reduce the time and labor required for component placement while minimizing the risk of human error.
Soldering Techniques
Creating Strong Connections
Once the components are positioned, the next step is soldering the connections between them. Soldering requires precision and control to ensure strong and reliable connections. Through-hole soldering, which involves inserting component leads through holes in the board and applying heat and solder, is a common technique. Another popular method is surface-mount technology (SMT) soldering, where solder paste is applied to component pads and reflowed using heat.
Advanced Soldering Methods
Wave and Reflow Soldering
Beyond through-hole and SMT soldering, several advanced techniques are used in PCB assembly. Wave soldering is ideal for PCBs with numerous components, allowing for high-speed processing and reduced labor costs. This method involves passing the PCB through a wave of molten solder, which flows over the components, creating strong bonds. Reflow soldering, another efficient technique, involves applying solder paste to component pads and heating the board to melt the solder.
Choosing the Right Technique
Tailoring to Specific Needs
The choice of soldering technique depends on the PCB’s specific requirements and the components involved. For instance, through-hole soldering is preferred for components with large leads, like connectors and switches. In contrast, SMT soldering is better suited for components with smaller leads, such as integrated circuits and capacitors. Wave and reflow soldering are often employed for high-volume production runs, processing large numbers of PCBs quickly and efficiently.
Material Selection
Ensuring Performance and Reliability
Material selection is critical in the PCB assembly and soldering process. The board material, component leads, and solder must withstand the high temperatures and stresses associated with soldering and the mechanical stresses and vibrations during the device’s operation. Choosing the right materials ensures the overall performance and reliability of the PCB.
Conclusion
PCB assembly and soldering are complex and highly specialized fields requiring a deep understanding of various techniques and materials. By selecting the appropriate techniques and materials, manufacturers can produce high-quality PCBs that meet required specifications and perform reliably across various applications. Whether you are a seasoned professional or new to the field, mastering PCB assembly and soldering techniques is vital for creating electronic components that meet the demands of modern electronics.
FAQs
Q: What is the role of automated placement machines in PCB assembly?
A: Automated placement machines significantly reduce the time and labor required for component placement and minimize the risk of human error, enhancing the efficiency and accuracy of the PCB assembly process.
Q: How does through-hole soldering differ from SMT soldering?
A: Through-hole soldering involves inserting component leads through holes in the board and applying heat and solder to create connections. In contrast, SMT soldering applies solder paste to component pads and reflows it using heat.
Q: What are the benefits of wave soldering?
A: Wave soldering allows for high-speed processing of PCBs with numerous components, reducing labor costs and creating strong bonds efficiently.
Q: When is reflow soldering most commonly used?
A: Reflow soldering is often used for high-volume production runs, where it can process large numbers of PCBs quickly and efficiently.
Q: Why is material selection critical in PCB assembly?
A: Material selection is crucial as it ensures the PCB can withstand high temperatures, stresses, mechanical stresses, and vibrations, maintaining performance and reliability throughout the device’s operation.