1. Detailed introduction to processing methods
CNC machining is a digitally controlled precision machining technology that controls the movement and operation of machine tools through computer programs, and can achieve high-precision, complex-shaped parts machining. For example, in the aerospace field, CNC machining is often used to manufacture engine blades, precision structural parts, etc.
3D PRINT metal printing is an additive manufacturing technology that builds parts by stacking metal materials layer by layer. It can produce complex geometric shapes that are difficult to achieve with traditional machining, such as parts with complex internal channels. For example, in the medical field, personalized orthopedic implants can be printed.
Punch stamping uses the impact force of the punch to deform the sheet in the mold to obtain parts of the desired shape and size. It is often used for mass production of simple-shaped metal parts, such as metal shells in automotive parts.
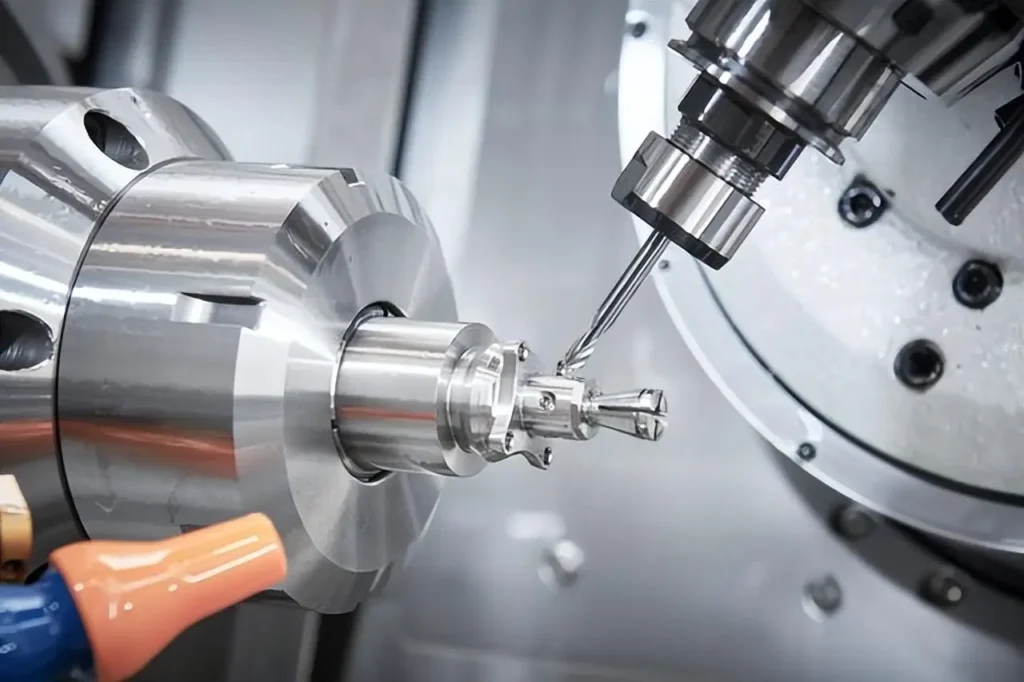