Introduction
In the world of modern electronics, Printed Circuit Board Assemblies (PCBA) form the backbone of a vast array of devices, from smartphones to advanced computing systems. As the intricacies of these devices grow, the necessity for stringent quality and reliability checks on PCBA becomes paramount. One critical method to achieve this is through comprehensive electrical testing and inspection, which helps in detecting defects and verifying the overall performance of the PCBAs.
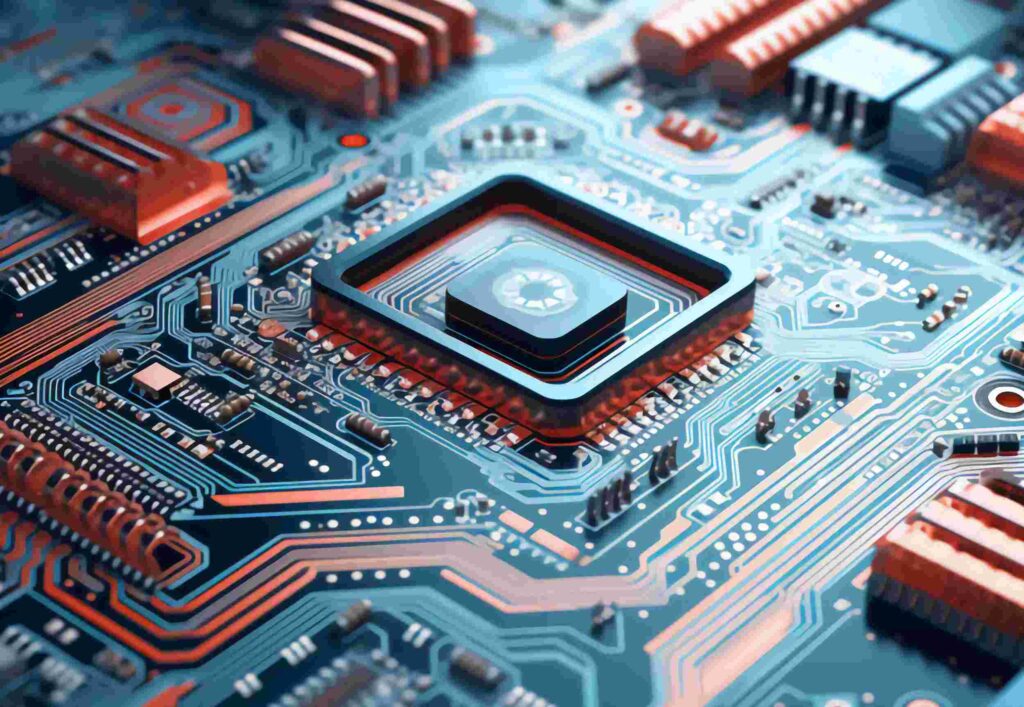
The Role of Electrical Testing and Inspection
Ensuring Integrity and Functionality
Electrical testing and inspection are vital processes in the quality assurance of PCBA. This process begins with a visual inspection to identify visible defects, such as cracks, scratches, or misaligned components. Following this, a series of electrical tests are conducted, including continuity, insulation, and functional testing. These tests collectively ensure the integrity and functionality of the PCBA.
Continuity and Insulation Testing
Verifying Electrical Paths and Insulation
Continuity testing is crucial as it confirms that the electrical paths on the board are complete and free from breaks or shorts. This is generally performed using multimeters or continuity testers that apply a low-level electrical current to the board, checking for resistance or continuity in the circuit. Insulation testing, conversely, ensures that there are no unwanted electrical connections between adjacent components or between the board and its surroundings, thus verifying the adequacy of the board’s insulation.
Functional Testing
Assessing Board Performance
Functional testing stands out as a critical component of electrical testing and inspection. This phase checks if the PCBA performs as expected by applying various inputs such as voltage, current, and data signals, and then measuring the corresponding outputs. Functional testing can be automated or manual, or a hybrid of both, to ensure comprehensive evaluation of the board’s performance.
Advanced Testing Technologies
Leveraging AOI and AXI
To complement traditional testing methods, modern PCBA manufacturers are increasingly utilizing advanced testing technologies like Automated Optical Inspection (AOI) and X-ray Inspection (AXI). AOI employs high-resolution cameras coupled with sophisticated software to detect defects such as solder bridges or misaligned components. AXI, on the other hand, provides a detailed view of the internal structure of the board, identifying issues such as shorts or opens that are not visible externally.
Conclusion
Electrical testing and inspection are indispensable in the PCBA manufacturing process, ensuring the quality and reliability of electronic products. By integrating traditional testing methods with advanced technologies, manufacturers can detect and rectify defects early, thus minimizing the risk of costly recalls and enhancing customer satisfaction. As electronic devices become increasingly complex, the significance of rigorous electrical testing and inspection will only intensify, cementing its role as a crucial element in PCBA production.
FAQs
Q: What is the importance of electrical testing and inspection in PCBA?
A: Electrical testing and inspection are essential for ensuring the quality and reliability of PCBA, helping to detect defects and verify the functionality of the board.
Q: What does continuity testing in PCBA involve?
A: Continuity testing verifies that the electrical paths on the board are intact, using equipment like multimeters to check for resistance or continuity in the circuit.
Q: How does insulation testing benefit the PCBA process?
A: Insulation testing ensures that the PCBA’s insulation is adequate, preventing unwanted electrical paths between components and their surroundings.
Q: What is the role of functional testing in PCBA?
A: Functional testing assesses the PCBA’s performance by applying various inputs and measuring the outputs to confirm the board functions as intended.
Q: What advanced technologies are used in PCBA testing?
A: Advanced technologies such as Automated Optical Inspection (AOI) and X-ray Inspection (AXI) are used to detect both external and internal defects in PCBA.