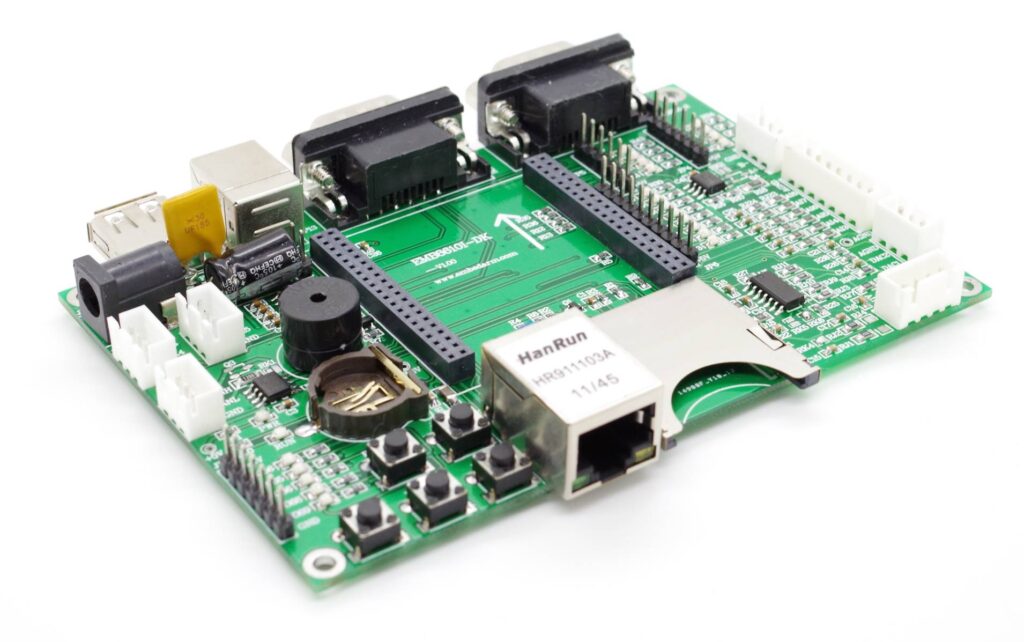
Introduction
Design for Manufacturing (DFM) is an integral part of Printed Circuit Board Assembly (PCBA) that focuses on optimizing the design process to facilitate efficient, cost-effective production of electronic products. As the electronics industry faces growing demands for cost reduction, product quality, and adherence to tight delivery schedules, DFM has emerged as a vital strategy for manufacturers to meet these challenges.
Importance of DFM in PCBA
Ensuring Cost-Effective and Reliable Production
DFM plays a crucial role in PCBA design by addressing various manufacturing constraints like component placement, routing, and assembly processes during the design phase. This foresight helps prevent costly rework, reduce waste, and enhance product reliability. For example, a design that simplifies the assembly process and reduces the reliance on complex components can substantially decrease production costs.
Component Selection in DFM
Balancing Performance and Availability
Selecting the right components is fundamental to the DFM process. The choice of components directly influences the PCBA’s performance, reliability, and cost. Designers must carefully select components that not only meet the technical specifications but are also readily available and easily sourced. This strategic selection prevents production delays caused by component shortages or long lead times.
Optimizing PCB Layout
Improving Signal Integrity and Thermal Management
A key element of DFM is the optimization of the PCB layout. A well-planned layout ensures components are arranged to minimize signal integrity issues, electromagnetic interference (EMI), and enhance thermal management. Designers use advanced design tools and techniques to simulate and analyze the PCB’s behavior under different operating conditions, leading to a more robust and reliable design.
Adhering to DFM Guidelines
Following Best Practices for Manufacturability
Utilizing DFM guidelines and best practices is essential in PCBA design. These guidelines offer a set of rules and recommendations that help designers ensure the manufacturability of their designs. By adhering to these standards, designers can avoid common design pitfalls and streamline the production process, ensuring that the PCBA meets the required specifications and quality benchmarks.
Conclusion
DFM is a critical component of PCBA design, contributing significantly to the production of high-quality, cost-effective electronic products. By considering manufacturing constraints, selecting appropriate components, optimizing PCB layouts, and following DFM best practices, designers can develop designs that are not only manufacturable but also meet stringent performance and reliability standards. As the electronics industry continues to evolve, the emphasis on DFM in PCBA design will only intensify, necessitating that designers remain current with the latest tools, techniques, and best practices.
FAQs
Q: What is Design for Manufacturing (DFM) in PCBA?
A: DFM in PCBA is a strategy that focuses on optimizing the design process to ensure the efficient and cost-effective production of electronic products by considering manufacturing constraints, component selection, and layout optimization.
Q: Why is component selection important in DFM?
A: Component selection is crucial because it affects the PCBA’s performance, reliability, and cost. Proper selection ensures that components meet technical specifications, are available, and can be easily sourced, preventing production delays.
Q: How does PCB layout optimization contribute to DFM?
A: PCB layout optimization improves signal integrity, reduces electromagnetic interference, and enhances thermal management. This is achieved by using design tools to simulate the PCB’s behavior under different conditions.
Q: What are DFM guidelines?
A: DFM guidelines are a set of rules and recommendations that help designers ensure the manufacturability of their designs, avoid common pitfalls, and streamline the production process.
Q: How does DFM impact the future of PCBA design?
A: As the demand for electronic products grows, the importance of DFM in PCBA design will increase, requiring designers to stay updated with the latest design tools, techniques, and best practices to meet industry standards.