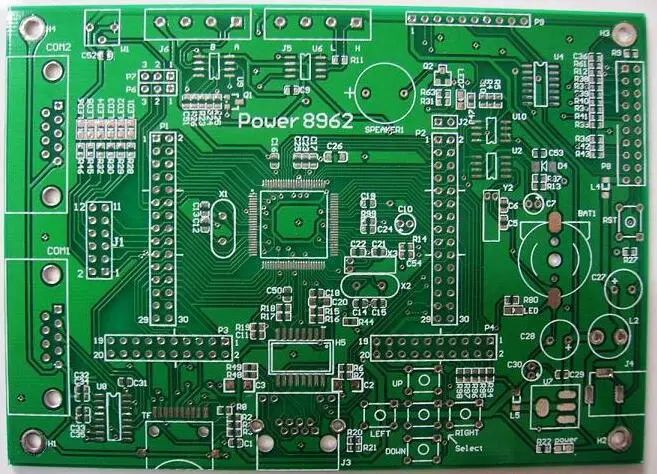
Introduction
Surface Mount Technology (SMT) has significantly advanced the field of PCB assembly, bringing numerous benefits that have transformed electronic device design and manufacturing. As electronic devices become more complex and compact, SMT has emerged as the preferred method for assembling printed circuit boards (PCBs). This article explores the key advantages of SMT and its impact on the electronics industry.
Increased Component Density
Maximizing Space Efficiency
One of the primary benefits of SMT is its ability to increase the density of components on a PCB. SMT allows manufacturers to place more components onto a smaller area, resulting in more compact and efficient devices. This capability has been instrumental in developing sophisticated electronics such as smartphones and laptops, where space efficiency is crucial.
Reduced Weight and Size
Optimizing for Compact Applications
Surface mount components are generally smaller and lighter compared to traditional through-hole components. This reduction in weight and size is particularly advantageous in applications where space and weight are critical, such as aerospace and defense. Additionally, SMT components are less likely to be damaged during handling and transportation, which minimizes the risk of component failure and lowers associated costs.
Improved Thermal Performance
Enhancing Heat Dissipation
SMT offers superior thermal performance over through-hole technology. Surface mount components have lower thermal resistance, which facilitates better heat dissipation and reduces thermal stress on the PCB. This is especially important in high-power applications like power supplies and motor control systems, where effective heat management is essential.
Faster and More Efficient Manufacturing
Streamlining Production
The adoption of SMT in PCB assembly leads to faster and more efficient manufacturing processes. Automated pick-and-place machines and reflow soldering techniques enable quick and accurate placement of SMT components. This automation reduces labor costs and assembly time, allowing manufacturers to scale production and meet increasing demand more effectively.
Enhanced Durability
Withstanding Harsh Conditions
SMT components are more resistant to vibration and shock compared to through-hole components. This durability makes them suitable for applications exposed to harsh environmental conditions, such as industrial control systems and automotive electronics. The improved resistance to mechanical stress enhances the overall reliability of the device.
Improved Reliability and Reduced Maintenance
Minimizing Failures
SMT also contributes to improved reliability and lower maintenance costs. Surface mount components are less prone to mechanical stress and fatigue, which decreases the likelihood of component failure and downtime. Additionally, SMT facilitates easier inspection and testing, enabling manufacturers to detect and address defects earlier in the production process.
Conclusion
Surface Mount Technology (SMT) has revolutionized PCB assembly, offering significant benefits that enhance the design and manufacturing of electronic devices. By enabling increased component density, reduced weight and size, improved thermal performance, and faster manufacturing processes, SMT has become a cornerstone of modern electronics. As the demand for more compact and sophisticated devices continues to grow, SMT will remain a vital technology in the electronics industry.
FAQs
Q: What are the main advantages of Surface Mount Technology (SMT) in PCB assembly?
A: SMT offers increased component density, reduced weight and size, improved thermal performance, faster and more efficient manufacturing, enhanced durability, and improved reliability.
Q: How does SMT improve thermal performance in electronic devices?
A: SMT components have lower thermal resistance, which allows for better heat dissipation and reduces thermal stress on the PCB.
Q: Why is SMT preferred for applications where space and weight are critical?
A: SMT components are smaller and lighter than through-hole components, making them ideal for compact and weight-sensitive applications.
Q: How does SMT contribute to faster manufacturing processes?
A: SMT enables quick and accurate placement of components using automated pick-and-place machines and reflow soldering techniques, reducing labor costs and assembly time.
Q: In what types of environments are SMT components particularly beneficial?
A: SMT components are more resistant to vibration and shock, making them suitable for harsh environments such as industrial control systems and automotive electronics.