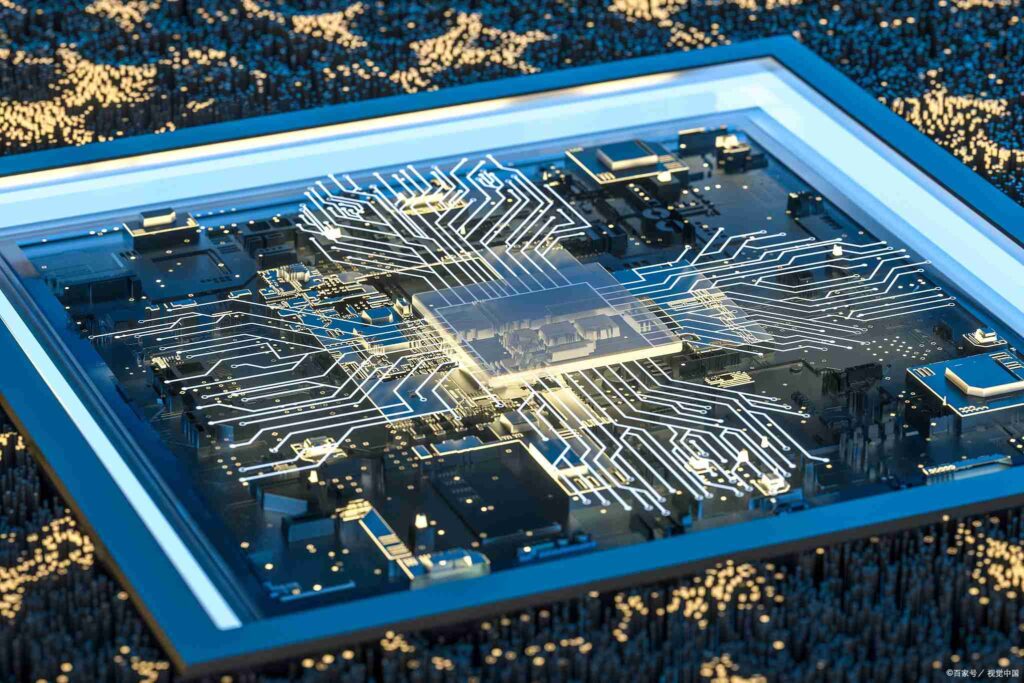
Introduction
PCB testing and troubleshooting methods are crucial steps in the development and production of printed circuit boards. Given their complexity, rigorous testing is essential to ensure functionality, reliability, and quality. This article explores various PCB testing and troubleshooting methods used to identify defects, verify performance, and ensure that the final product meets the required standards.
Determining the Testing Requirements
Identifying the Appropriate Testing Methods
The first step in PCB testing is determining the type of testing required. This depends on the PCB’s type, intended application, and the level of quality control needed. Testing methods include visual inspection, electrical testing, and functional testing. Visual inspection checks for defects like cracks, scratches, and oxidation. Electrical testing measures the PCB’s electrical characteristics, such as resistance, capacitance, and inductance. Functional testing assesses the PCB’s performance under various conditions like temperature, humidity, and vibration.
In-Circuit Testing and Boundary Scan Testing
Comprehensive Testing Techniques
In-circuit testing (ICT) is one of the most common PCB testing methods. It involves connecting the PCB to a test fixture and applying electrical signals to test its components and connections. ICT is particularly effective for PCBs with complex circuits and multiple components. Boundary scan testing (BST) is another method used to verify the integrity of a PCB’s connections through its boundary scan ports, ensuring the correct operation of its circuitry.
Troubleshooting Defective PCBs
Identifying and Resolving Issues
PCB troubleshooting is a critical part of the testing process, essential for identifying and resolving issues when a PCB does not function as expected. This involves analyzing the PCB’s design, manufacturing process, and testing results. Troubleshooting methods include visual inspection, electrical testing, and functional testing, similar to the initial testing methods, to identify and address any defects.
Simulation and Advanced Tools
Utilizing Technology for Precision
The use of simulation software is an important aspect of PCB testing and troubleshooting. Designers can simulate their PCB’s behavior before manufacturing, identifying potential design flaws and making necessary adjustments. Simulation software can also simulate various testing scenarios, allowing designers to predict the results of different testing methods. Alongside simulation, specialized tools and equipment, such as oscilloscopes, logic analyzers, and signal generators, play a crucial role in PCB testing and troubleshooting.
Conclusion
PCB testing and troubleshooting are essential steps in the development and production of printed circuit boards. By employing various testing methods and troubleshooting defects, and using simulation software and specialized tools, designers and manufacturers can ensure that their PCBs meet the required standards and perform as expected. Understanding these methods is vital for producing reliable and high-quality electronic components.
FAQs
Q: What is the purpose of in-circuit testing (ICT) in PCB testing?
A: In-circuit testing (ICT) connects the PCB to a test fixture and applies electrical signals to test the components and connections. It is effective for testing PCBs with complex circuits and multiple components.
Q: How does boundary scan testing (BST) work?
A: Boundary scan testing (BST) verifies the integrity of a PCB’s connections by testing its boundary scan ports, ensuring the correct operation of its circuitry.
Q: Why is simulation software important in PCB testing?
A: Simulation software allows designers to simulate PCB behavior before manufacturing, helping to identify potential design flaws and adjust accordingly, and simulates various testing scenarios for prediction purposes.
Q: What specialized tools are used in PCB testing and troubleshooting?
A: Specialized tools include oscilloscopes for measuring electrical signals, logic analyzers for analyzing digital signals, and signal generators for generating test signals for the PCB.
Q: What are the common defects looked for during PCB visual inspection?
A: Common defects include cracks, scratches, oxidation, and other visible issues that may affect the PCB’s performance.